Your Local Service & Repair Team
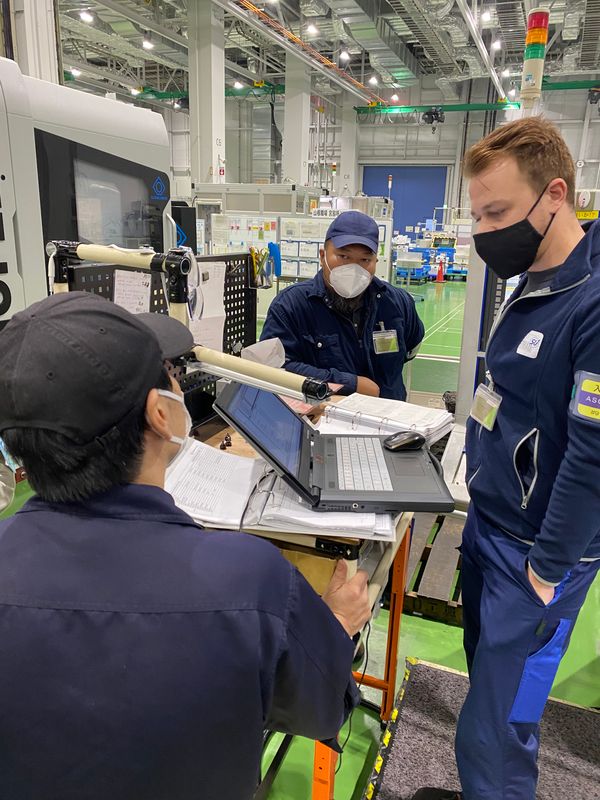
Combination of Mechanical skill and Customer Relation skill
Our pool of knowledge surrounding machine tool performance and accuracy is superior quality. This skill base gives us a competitive edge which is reflected in the high level of service we provides to our clients. We’re not just a service provider; we pro-actively works with clients to develop tailor-made solutions for both generic and unique technical problems.
The long-term relationships that this engenders results in a much greater understanding of a customer’s needs. This in turn ensures that Seibu Shoko delivers the optimum service package; providing repair, training and maintenance support.
-
Corrective Maintenance
-
Preventive Maintenance
-
Predictive Maintenance
Diverse Team
Our team are consists of various background of countries and skills. We can deliver our services in Japanese, English, Bahasa Indonesia and Bahasa Malaysia. Also we are now exploring for Thai and Vietnamese.
Total Package of Services
We offer not only service & repair program, but also with spare parts preparation and management. This helps our client to minimize the amount of capital blocked in inventory while ensuring the timely availability of spare parts.
Reliability Centered Services
We refer to the machine OEM itself as much as possible to maintain the original machine functions and operation. This may include replacement, redesigning or even decommissioning of the machine tool.
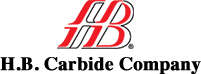
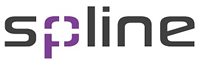
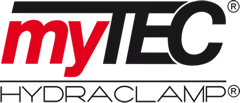

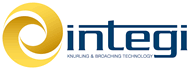
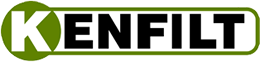
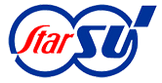
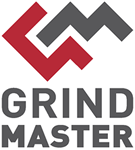
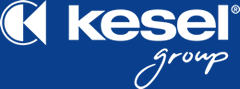
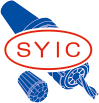
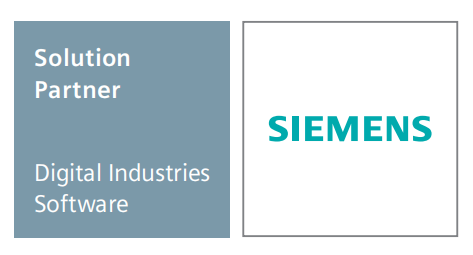
Approved Partner of Siemens
Seibu Shoko are proud of our accreditation as an official partner for Siemens. Before accepting companies as partners, Siemens ensure that we must prove our capabilities. Only then do Siemens certify Optima according to rigorous, globally uniform standards, systematically supporting and enhancing us using the same criteria Siemens apply to the training of their own employees.
Our Skills
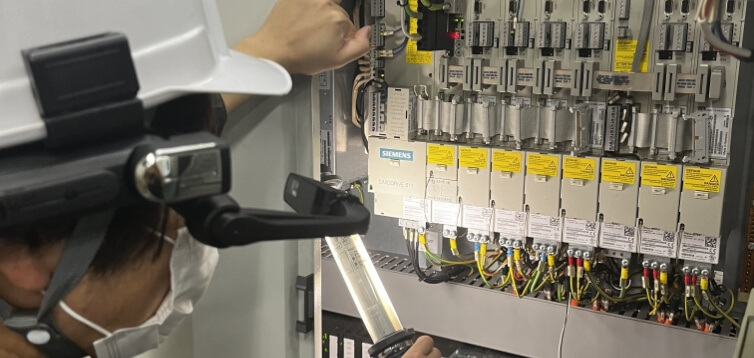
PLC/CNC & Electrical Unit
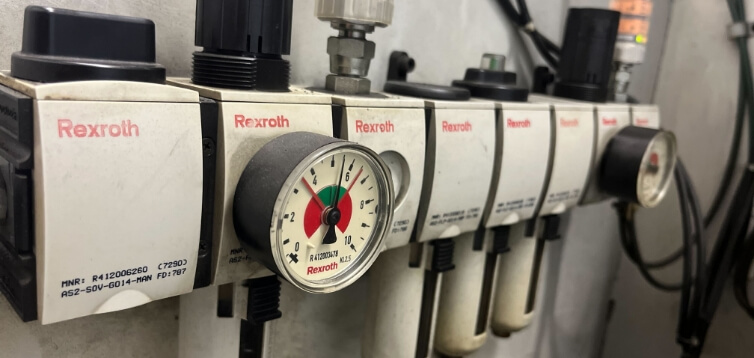
Pneumatic Unit
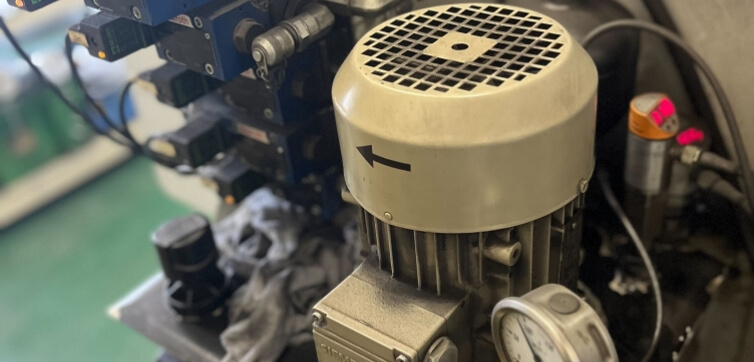
Hydraulic Unit
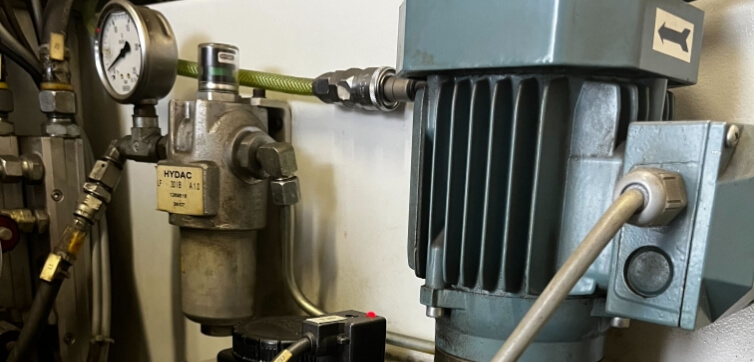
Lubrication Unit
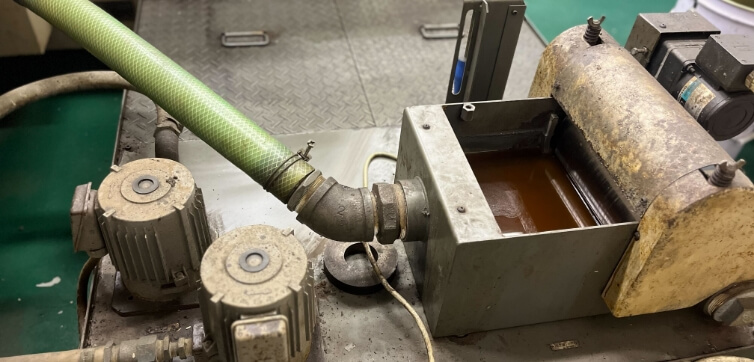
Cooling Unit
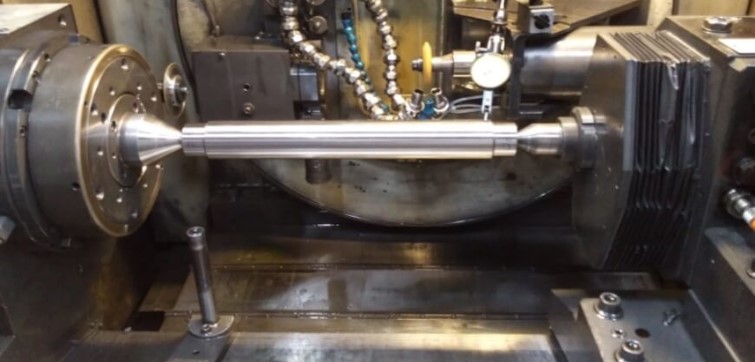
Mechanical
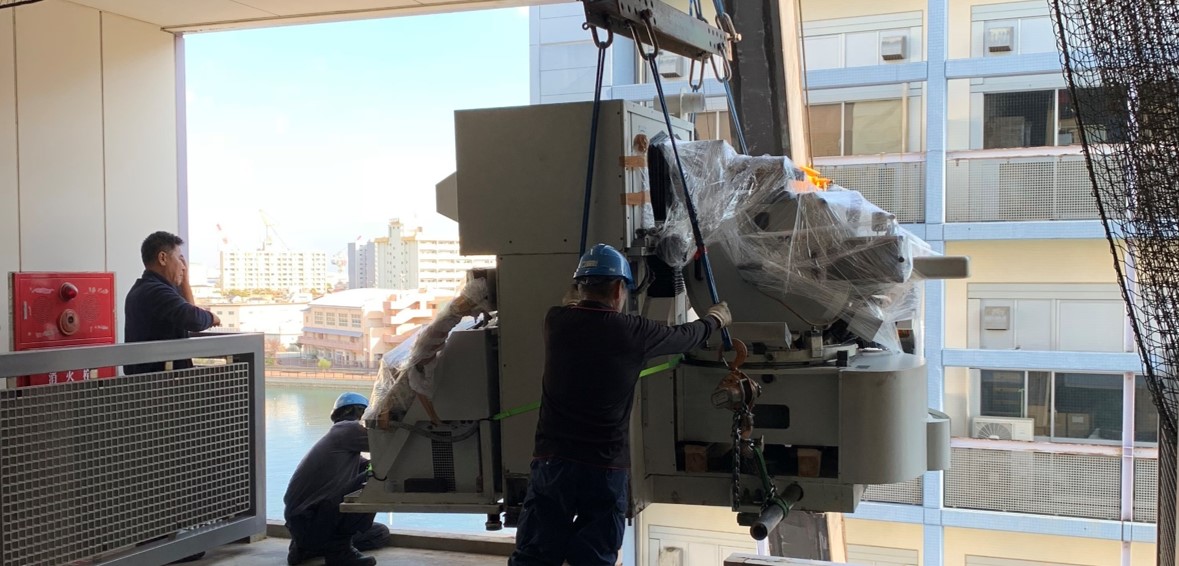
Machine Relocation
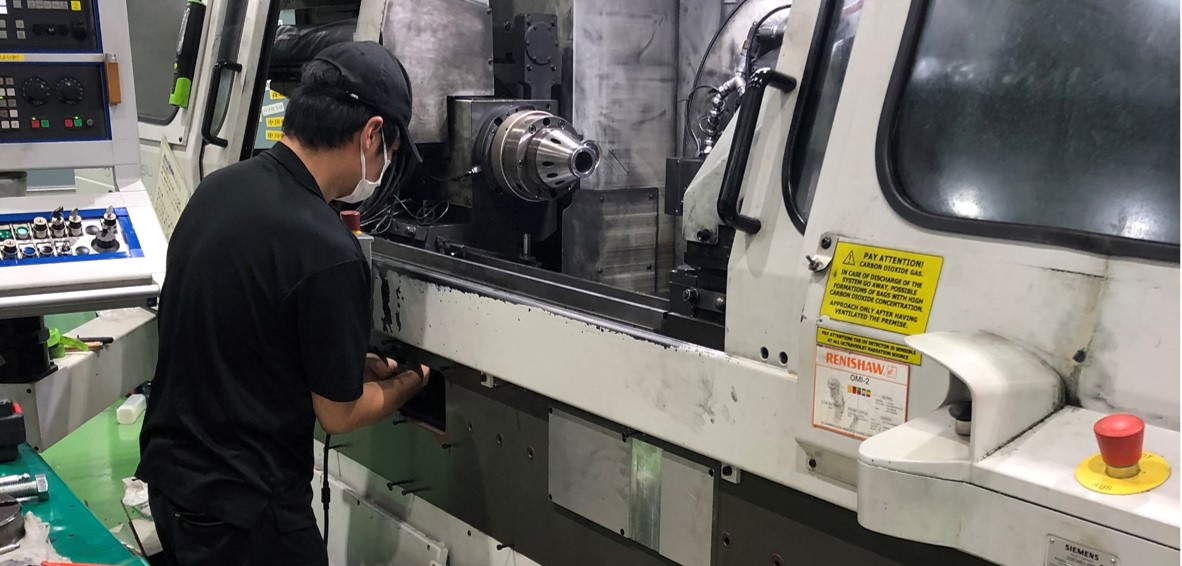
Retrofit
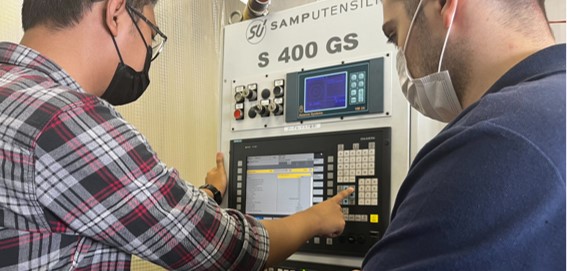
Maintenance Training
Frequently Asked Questions
We lost a lot of drawings and documents. Will you still help us?
Drawings and documents are one of the many tools that important to a machine tool. However, before you giving up, lets have a discussion! We will think a way for you.
Our team don't speak Japanese/English
Our engineer team able to communicate in Japanese, English, Bahasa Melayu and Bahasa Indonesia. We also have a team dedicated to interpreting services for Vietnamese and Thai. Fell free to contact us if you would like to request other languages.
My machine is more than 20 years old and the OEM itself does not exist anymore.
Usually, for an old machine, we would recommend for a retrofitting. It is because retrofitting provides ability to revitalize the machine with new controls, thus giving the machine a longer service lift.